デジタルツインとは、現実のモノやプロセスを仮想空間で再現し、リアルタイムでデータを反映させる技術です。
製造業においては、この技術を活用することで、生産プロセスの効率化やコスト削減が実現され、競争力を強化することが可能です。
本記事では、デジタルツインの基本概念から製造業での具体的な活用事例、そしてもたらされるメリットまでを詳しく解説しますので是非最後までご覧ください。
製造・建設・物流業界の業務効率化と安全性を高める「デジタルツイン」
サービスの特徴や国内外の事例をまとめた資料をご用意しました。
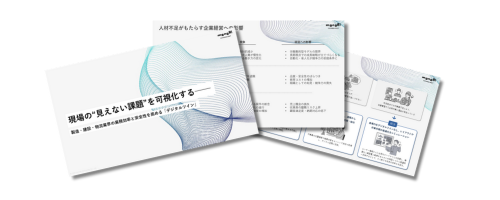
デジタルツイン活用事例集の無料ダウンロードはこちら
資料をダウンロードする|デジタルツインとは
デジタルツインとは、物理的資産やプロセスをデジタル空間に再現する技術であり、リアルタイムデータを基にした仮想モデルのことを指します。
この技術は、IoT(モノのインターネット)やAI(人工知能)と組み合わせることで、現実世界の状況を正確にシミュレーションし、さまざまな分析や予測を行うことが可能です。
デジタルツインは、物理モデルとその仮想モデルとの接続が重要であり、この接続はセンサーによって生成されるリアルタイムデータによって確立されます。
これにより、製品ライフサイクル全体にわたる動的な仮想表現が実現し、製造業や都市計画などのさまざまな分野で活用されています。
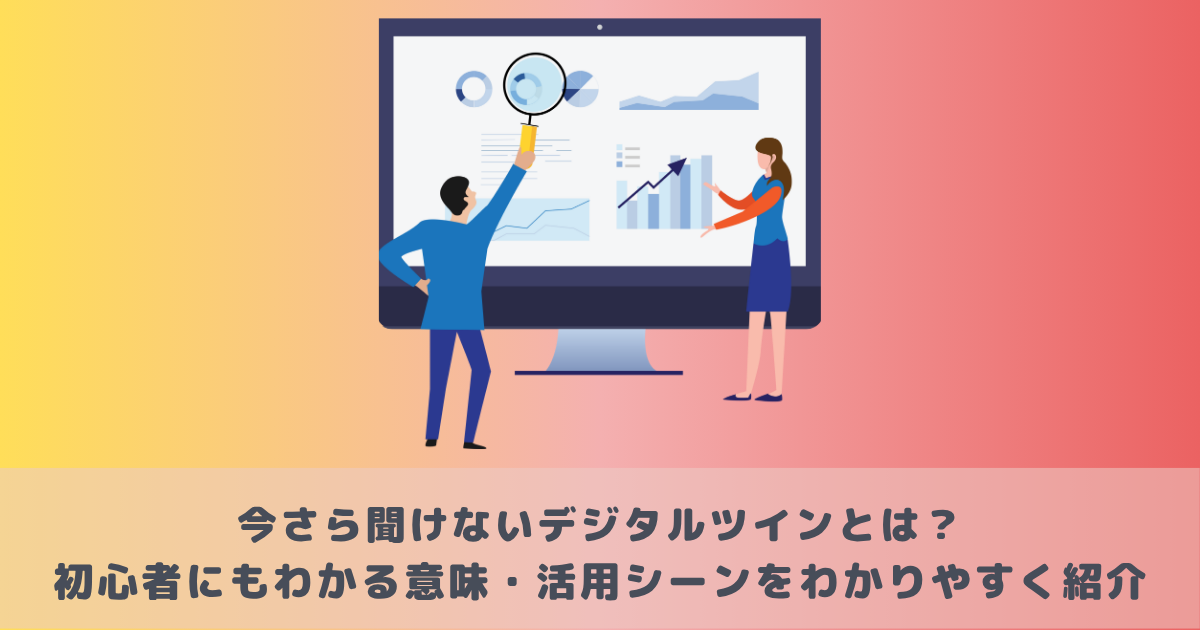
|製造業でデジタルツインはどのように活用されている?
製造業において、デジタルツインは製造プロセスや製品ライフサイクルの効率化、品質向上を目的とした幅広い活用が進められています。
この技術は、設計段階から製造、運用、保守に至るまで、あらゆるプロセスで価値を提供しています。
製造プロセスの最適化
デジタルツインは、製造ラインの動きを仮想空間で再現し、問題点や改善点を可視化します。
これにより、以下のようなメリットが得られます。
- 生産工程のボトルネックを特定。
- リアルタイムで設備の稼働状況を監視。
- 無駄なコストや時間を削減。
例えば、スマートファクトリーの構築において、デジタルツインを活用することで、試作品を作成せずに製造プロセスの最適化を行うことが可能です。
製品設計と開発の効率化
製品の設計段階では、デジタルツインが仮想モデルを用いて性能や耐久性の検証を行います。
これにより、開発コストや時間を削減しつつ、品質向上を実現します。
- 設計変更をシミュレーションで確認。
- 製品のテスト回数を大幅に削減。
- 顧客の要望に迅速に対応。
たとえば、車両設計において、デジタルツインを活用することで、空力性能や安全性を効率的に検証できます。
設備のメンテナンスと予知保全
製造設備にセンサーを設置し、デジタルツインで稼働データを分析することで、設備の故障を未然に防ぐ「予知保全」が可能となります。
- 設備の寿命を延ばす。
- 生産ダウンタイムを削減。
- 故障の原因を迅速に特定。
例えば、航空機エンジンのメンテナンスでは、デジタルツインを活用して部品の劣化状況をモニタリングし、最適なタイミングでの交換が行われています。
サプライチェーンの最適化
デジタルツインは、サプライチェーン全体のデータを統合し、最適な供給計画や在庫管理を支援します。
- 原材料や部品の供給状況を可視化。
- 最適な生産スケジュールを策定。
- コスト削減と供給リスクの回避。
例えば、製造業大手は、デジタルツインを用いた需要予測システムを導入することで、迅速な意思決定を可能にしています。
|デジタルツインを製造業に活用するメリット
デジタルツインを製造業に活用するメリットは多岐にわたります。
以下に主なメリットを詳しく解説します。
1. 品質の向上・リスクの削減
デジタルツインを活用することで、製品やプロセスのシミュレーションが可能となり、事前に品質の問題を特定できます。
これにより、製品の品質が向上し、不良品の発生を減少させることができます。
また、仮想環境での試験により、新製品開発時のリスクも大幅に低減されます。
2. オペレーションの効率化・標準化
デジタルツインは、生産ラインの運用状況をリアルタイムで監視し、トラブル予測や故障防止に役立ちます。
これにより、オペレーションが効率化され、作業手順の標準化が進むことで、生産性が向上します。
3. シミュレーションによるリードタイムやコストの削減
デジタルツインを利用することで、物理的な試作や検証にかかる時間とコストを大幅に削減できます。
仮想空間でのシミュレーションによって、迅速な製品開発が可能になり、試作回数を自由に増やすことができるため、最適な設計を見つけやすくなります。
4. アフターサービスの充実
デジタルツインは、製品が市場に出た後もその性能を監視することができるため、アフターサービスの質を向上させることができます。
顧客からのフィードバックをリアルタイムで反映し、必要な改善策を迅速に講じることが可能です。
5. 技術の継承
デジタルツインは、熟練した技術者から新しい従業員への技術伝承を効率的に行うためのツールとしても機能します。
仮想環境でのトレーニングやシミュレーションによって、新人でも短期間で必要なスキルを習得できるようになります。
これらのメリットにより、製造業はデジタルツイン技術を導入することで競争力を高め、市場での優位性を確保することが期待されています。
|製造業のデジタルツイン活用事例
デジタルツインは、製造業のさまざまな分野で導入が進んでおり、各企業が独自の方法でこの技術を活用しています。
BMW:3Dスキャンによる工場メタバース化
BMWは、世界中の自動車工場を3Dスキャンし、デジタルツインを用いてメタバース化を進めています。
この取り組みにより、工場の設計や運用を仮想空間でシミュレーションし、効率的な生産ラインの構築が可能となっています。
3Dモデルによって、リアルタイムでのプロセス監視や改善点の特定が行えるため、生産性が向上しています。
旭化成:遠隔指導による従業員負担軽減
旭化成では、プロセス設備のデジタルツインを活用し、遠隔地からの運転監視や指導が実現されています。
特に「福島水素エネルギー研究フィールド」では、熟練者が現場に出向かずともリモートで状況を把握できるシステムを構築し、安全性と生産性の向上に寄与しています。
この技術により、従業員の負担が軽減されるとともに、専門知識を持つ人材の有効活用が図られています。
テスラ:車両自動アップデートシステム
テスラは、自社製品にデジタルツイン技術を導入し、車両のソフトウェアを遠隔で自動アップデートするシステムを構築しています。
この取り組みにより、ユーザーは常に最新の機能やセキュリティパッチを受け取ることができ、車両の性能向上が図られています。
ダイキン:製造ラインのロス削減事例
ダイキンは、自社の堺製作所臨海工場でデジタルツイン機能を搭載した新しい生産管理システムを開発しました。
このシステムでは、生産ラインの停止原因を事前に予測し、迅速な対応が可能となっています。
デジタルツインによって工程状況が可視化され、製造ラインのロス削減が実現されています。
日立:生産時間短縮を実現したデジタルツイン構築
日立は、大みか事業所で製造ラインのデジタルツインを構築し、生産時間を50%短縮することに成功しました。
RFIDタグやビデオカメラによって人とモノの流れを可視化し、生産進捗や品質改善に役立てています。
この取り組みにより、効率的な生産管理が実現されています。
トヨタ自動車:デジタルツインによる生産性向上
トヨタ自動車は、生産ライン全体をデジタルツインで管理することで、生産性向上とコスト削減を目指しています。
リアルタイムでのデータ分析に基づく意思決定が可能となり、迅速な対応が実現されています。
シーメンス:デジタルエンタープライズの実現
シーメンスは、自社製品やサービス全体にわたってデジタルツイン技術を適用し、一貫したエンタープライズソリューションを提供しています。
顧客向けに体験施設「DEX Tokyo」を開設し、実際にデジタル化ソリューションやロボット導入前後のイメージを具体的に把握できる機会を提供しています。
デンソー:自動車部品のデジタルツイン活用
デンソーでは、自動車部品ごとにデジタルツインモデルを作成し、その性能や生産プロセスを最適化しています。
この取り組みにより、高品質な部品供給と効率的な製造プロセスが実現されています。
これらの事例からもわかるように、製造業におけるデジタルツイン技術は、生産性や品質向上だけでなく、従業員の負担軽減にも寄与しています。
今後もこの技術は進化し続け、多くの企業でさらなる活用が期待されます。
|まとめ
製造業におけるデジタルツインの活用は、企業に多くのメリットをもたらしています。
現実世界のデータを仮想空間に反映することで、製品設計から製造、運用、保守に至るまで、あらゆるプロセスの効率化と最適化を可能にします。
デジタルツインは今後も進化し続け、多くの企業でさらなる活用が期待されるでしょう。
製造・建設・物流業界の業務効率化と安全性を高める「デジタルツイン」
サービスの特徴や国内外の事例をまとめた資料をご用意しました。
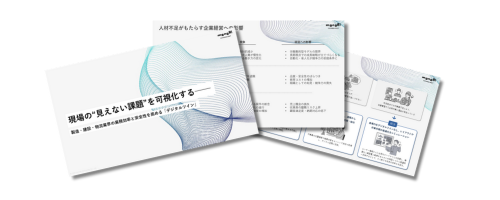
デジタルツイン活用事例集の無料ダウンロードはこちら
資料をダウンロードする